Range of services
based on 50 years of experience and expertise in textile calender construction
My offer to you individually adapted to market requirements
DIGITAL TRANSFORMATION
The days of employing analogue technology to progress the textile finishing process are long gone.
Textile finishing's metering industry has "emigrated" throughout the years.
Turkey, the Near and Middle East, and Asia have an advantage: a significantly different wage level, as well as a dumping tax and duty policy, are far superior than our proven textile finishing.
However, creative thinking, adaptation to small quantities, digital recording and management of process flows, and reproducibility of machine settings in all settings to be managed are all on the agenda.
As your consultant, I assure you digital thinking, inventive thinking about process flows, and implementation!
DIGITAL BUSINESS CONSULTING
Is the technology of today's dictum. In a competitive comparison, the equipment supplier's reaction time to changing customer and market requirements is critical.
I'd be delighted to assist you in expanding the options for adding value to the necessary process automation.
In the event of a recurrence, what the found process configuration provided in terms of performance yesterday must be raised at the touch of a button. All of the calender's actuators that need to be controlled can be operated digitally.
It's critical to keep track of your recipes.
In a competitive comparison, the various control approaches will be examined.
Where has this topic already been adopted, applied, and used for the advantage of customers?
When comparing the options available, these are the questions to consider.
SYNCHRONIZATION OF PROCESSES
What happens if the process rollers have vastly varied widths in a multi-motor drive?
Is it sufficient to focus on synchronous speeds?
What appears to be self-evident in athletics must also be applicable to mechanical engineering.
The outer runner in the race begins visually ahead of the inner runner, and the courses are pre-adjusted.
This must be taken into consideration in the calendar control as well.
Trains carrying products must be examined, synced, kept stable throughout the journey, and digitally controlled. I am your counselor from the beginning due to my knowledge of the technology and typical processes.
INTERVAL CONTROL OF MAINTENANCE PROJECTS
A precisely adjusted maintenance interval control is required for sophisticated calender systems. It is the notification signal of imminent defects, not the timing, that is the indication for repair.
If a malfunction is about to develop, maintenance must step in. Optical and auditory signals are to be conveyed. From the common textile finishing calender, modern manufacturers have produced a very sensitive working instrument that ensures long-term business success.
The Ramisch success mantra is to take precautions, not to defend errors, but to fix them first, then discuss them, not the other way around. Look find the guilty before retaliating; that would be corporate management at the expense of customers.
The RAMISCH philosophy
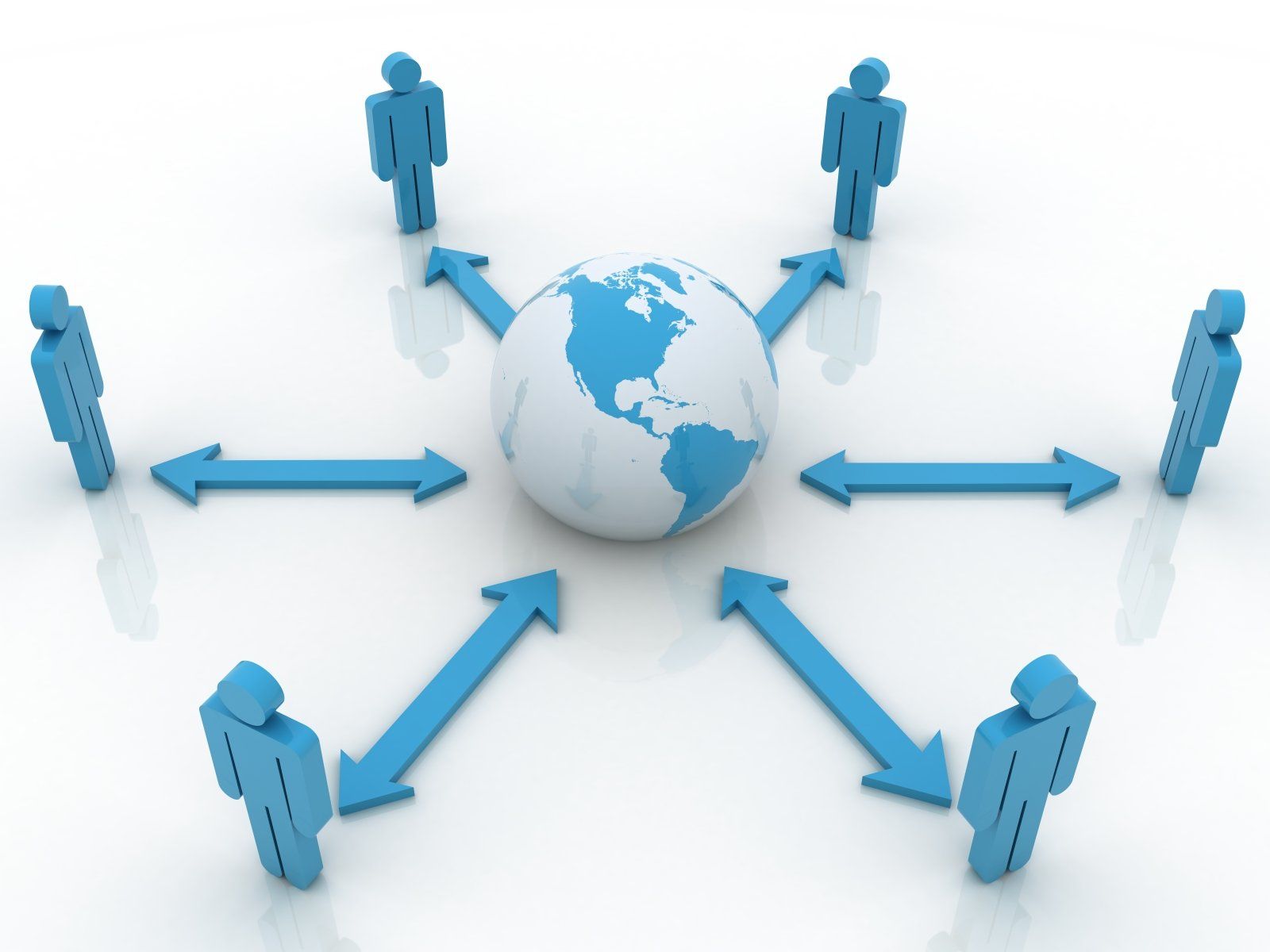
Quality

Efficiency
